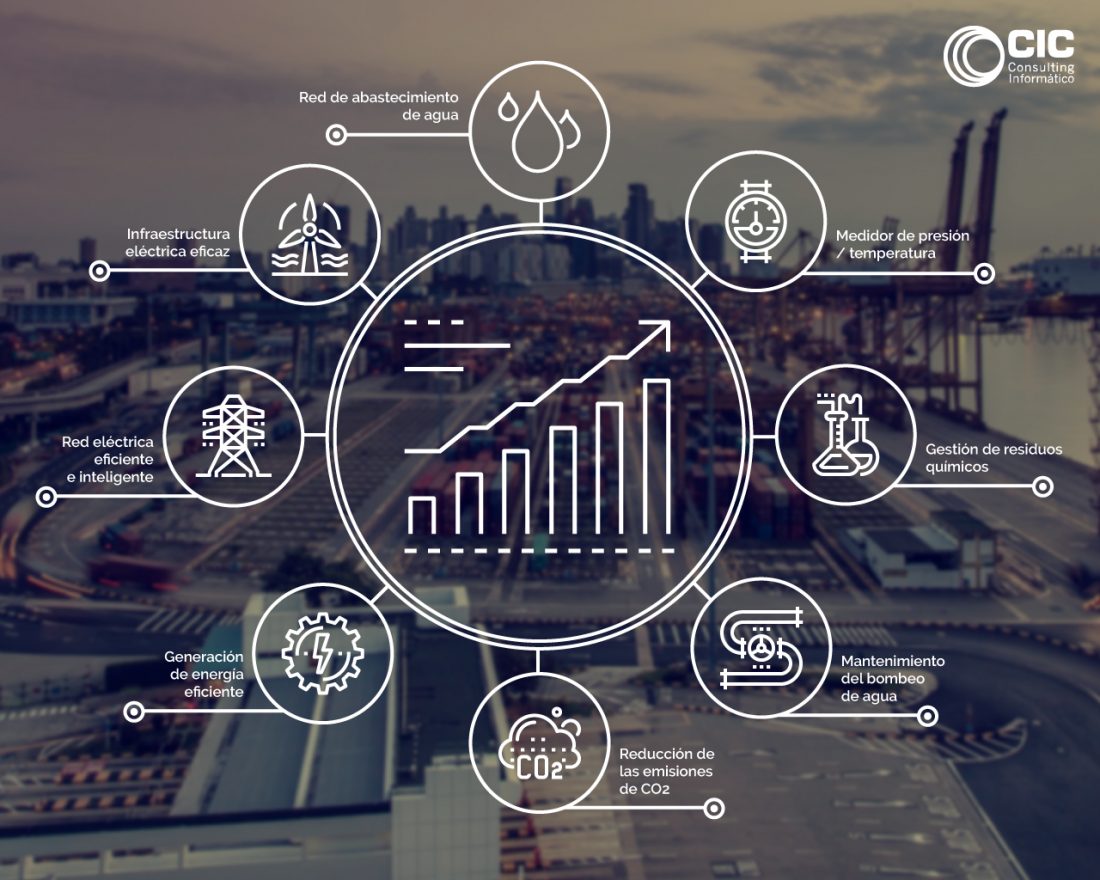
Cognitive technologies, that is to say, those that have the capacity to receive information, process it and obtain knowledge through experience, as well as, cloud computing have brought forth a new industrial era.
CIC Consulting Informático uses the analysis from a huge database, turning it into valuable information, which helps increase operational efficiency to industry. We develop innovative services to improve business processes in the industrial sector. Using IoT data from sensors and other devices, we can react quickly, make better decisions and understand how to optimize product or team’s performance.
As a technical base, CIC has created a system of analysis and monitoring that connects all elements and related machines to processes, and uses great quantities of data to offer a better product to our clients.
In production processes, if not detected, small problems can quickly turn into costly setbacks. One does not have the luxury of leaving equipment and vital processes unattended at night, or on weekends or bank holidays. At CIC we understand that in any environment, the most minute variable can be disastrous if left unattended and consequently be very costly.
Industrial Monitoring Software (IIoT)
If we talk about Industrial Monitoring it is because there is Industrial Software. Monitoring is no more than checking the state of any system or machine. Regular monitoring of machines makes the task of seeing if they need maintenance or not, easy.
A new term has been coined, the IIoT or Industrial Internet of Things. We can define IIoT as a multitude of technologies, applications, processes, methods and functions that can help in grouping together, manipulating and administering information on a large scale. Aimed at productive processes, it allows for the operation of intelligent machines, computers and robots, working together to improve productivity. It can be applied to fabrication, construction, mining, textile mills, chemical products plants, food processing and even service providers, such as telecoms, that use industrial software more and more.
In this increasingly competitive world, factories can not allow productive processes to wait or be interrupted due to problems. For example, a hydroelectric power plant, that keeps us warm in the winter, has to correct an error in the shortest time possible to not interrupt service to its clients. Therefore, the need to have a guaranteed production process, and more importantly, be able to react preventively in the optimization, repair, and maintenance of its equipment and production lines, minimizing downtimes.
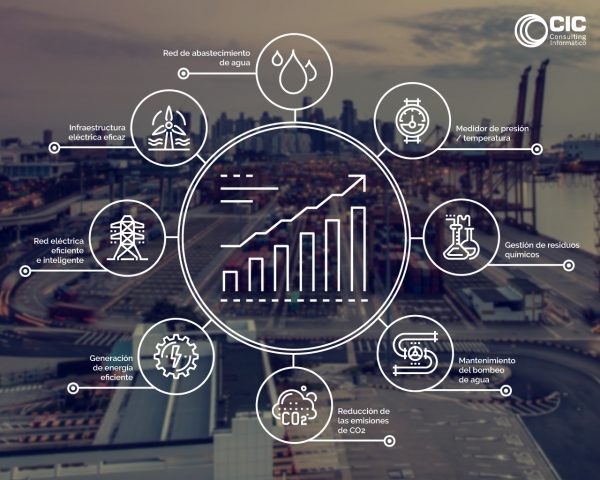
Benefits of IIoT for the monitoring of industrial processes
Cloud storage for huge quantities of data:
Did you know that a wind turbine is monitored 2000 times a minute? it provides one terabyte of data per week. Every manufacturer has a data center and various servers dedicated to collecting data and processing it. Normally, in the oil and gas industry, data centers are located far away from their installations. IoT uses cloud computing and stores huge quantities of data. The more computers and equipment that is connected, the more data is generated. These companies can store huge volumes of data and optimise their capacity to do so.
Learning automatically – Machine Learning
Machine Learning is another technology that uses great quantities of data. For example, a predictive device can detect a vibration in a machine and analyse it, or it can detect cracks in a drilling machine. If a company received data from only one source, the process would take years to complete. With IoT technologies, one can gather data simultaneously from several machines making the process a speedier one. Also, the diversified data from various machines can increase the precision and functionality of the predictive model.
The predictive maintenance tasks of IoT carry out analyses of equipment. Operators can pre-program the equipment for the next shift. IoT´s predictive maintenance tasks take into account the condition of the machines to detect changes that will be a problem in the future. IoT, therefore, guarantees effective maintenance in production processes.
Remote Monitoring
IIot uses intelligent monitoring of hundreds of machines from a single place. It does not need access to the machines. In the oil and gas industry, as well as in most utility companies, monitoring is remotely done and based on IoT.
IIoT facilitates the supervision of installations remotely, like pipes and drilling equipment. IIoT gathers data on the “health” of machines and equipment. This data is transferred to the cloud for future processing.
Minimizing Downtime
IoT reduces downtime and effectively uses resources for proper maintenance, this is especially true in the auto industry. IoT controls the state of the car, from the temperature of the engine, any vibrations it may have to fuel consumption.
Monitoring and control of industrial machinery: Conclusions
The industrial sector is optimizing the use of IoT to reduce downtimes on machinery and maintain them before problems arise. The monitoring by companies is based on IoT for better overall performance.